T Slot Aluminum Profiles
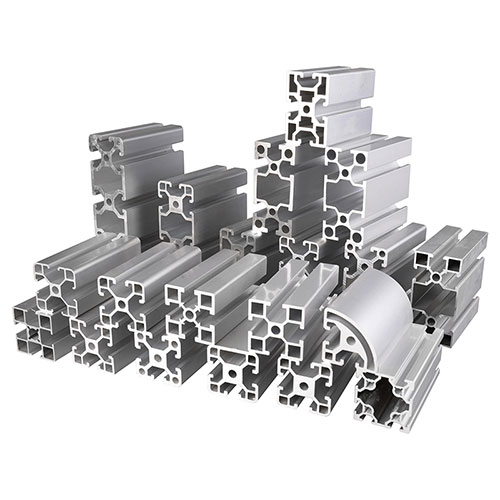
With T-Slot Aluminum, you get more value than you ever would with welded steel. Need flexibility? You’ve got it with t-slot aluminum. Need Versatility? Extruded aluminum has that too. Strong in the hot or the cold, corrosion resistant, extruded aluminum has everything you need to get a project done quickly and efficiently. No need to paint or weld unlike steel parts. Get whatever you need built fast and strong with our metric series profiles of extruded aluminum framing.
What kinds of shapes are there for the aluminum alloy profiles in the market?
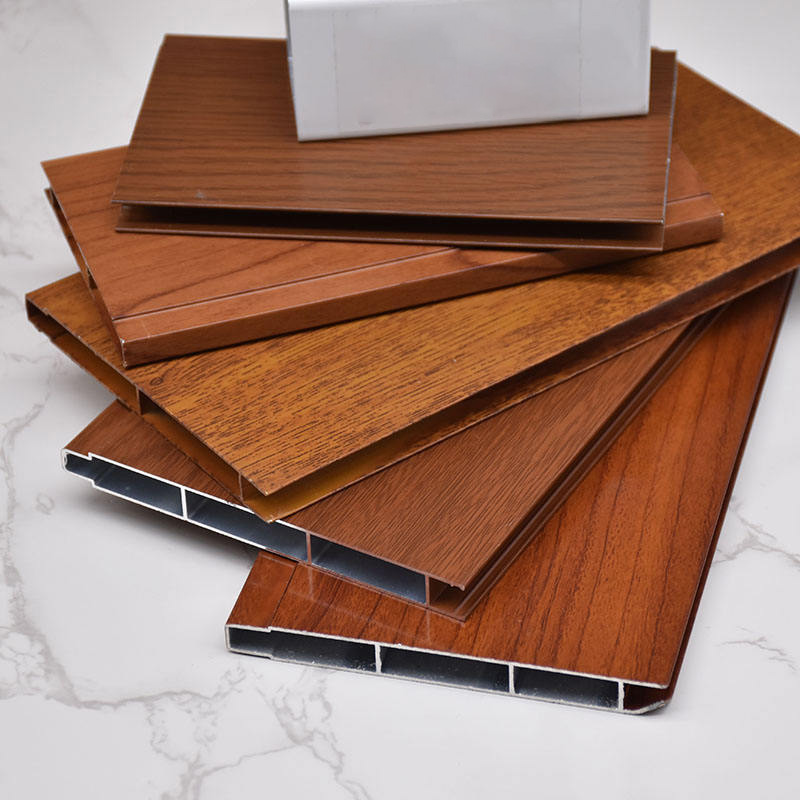
Standard profiles: These profiles are made of 1050, 1070, 3103 and 6060 aluminum alloys. They are available in reel and bar form and are manufactured to standardized shapes, sizes and dimensional tolerances.
These profiles are mainly used for door and window frames (facade structures). They are also useful in railings, balconies and other similar applications.
The differences between AL6061, AL6063 and AL6005
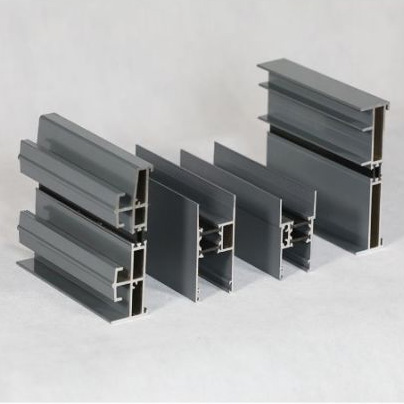
6063 is a low alloyed Al-Mg-Si high plastic alloy. It has many valuable characteristics:
1.Heat treatment strengthening, high impact toughness, insensitive to gaps.
2.It has good thermoplasticity, which can be extruded into various profiles with complex structure, thin wall and hollow at a high speed, or forged into forgings with complex structure. The quenching temperature range is wide and the quenching sensitivity is low. After extrusion and forging demoulding, as long as the temperature is higher than the quenching temperature, it can be quenched by spraying water or through water. Thin-walled parts (δ<3mm) can also be air-quenched.
3.Excellent welding performance and corrosion resistance, no stress corrosion cracking tendency, in the heat treatment can strengthen the aluminum alloy, Al-Mg-Si alloy is the only alloy that has not found stress corrosion cracking phenomenon.
4. The surface after processing is very smooth and easy to anodize and color. The disadvantage is that after quenching, if it is parked at room temperature for a period of time, it will have an adverse effect on the strength in aging (parking effect).
The application of wood grain aluminum profiles
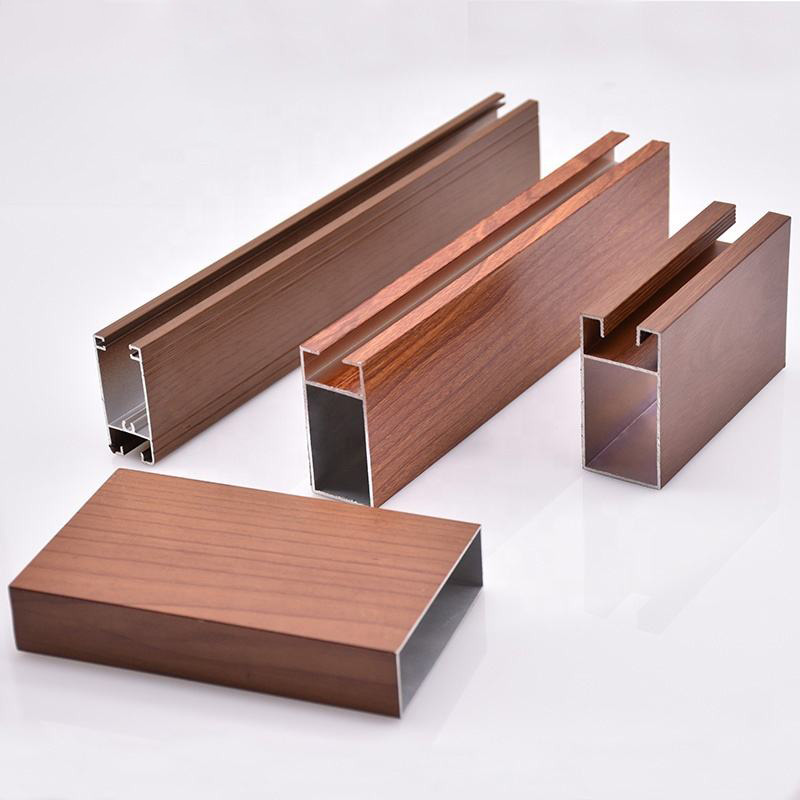
he application of 500-word wood grain aluminum profiles can be found in various fields. Here are a few examples:
1. Architecture: Wood grain aluminum profiles are used in the construction of buildings, particularly for doors, windows, and curtain walls. The wood grain finish gives the appearance of natural wood, providing a warm and aesthetic touch to the building’s exterior.
2. Interior Design: Wood grain aluminum profiles are commonly used for interior decoration and furniture. They can be used for wall paneling, ceilings, partitions, and cabinets, offering a stylish and durable alternative to traditional wooden materials.
3. Industrial Applications: Wood grain aluminum profiles are used in the manufacturing sector for various purposes. They can be used to create frames for solar panels, automotive trim, and electronic enclosures, among other applications. The wood grain finish adds an attractive design element to these products.
4. Retail and Commercial Spaces: Wood grain aluminum profiles find applications in retail stores, restaurants, and other commercial spaces. They can be used for display fixtures, signage, and storefronts, creating a modern and inviting ambiance.
5. Transportation: Wood grain aluminum profiles are used in the transportation industry for both interior and exterior applications. They can be used for decorative trims in vehicles, such as buses, trains, and boats, offering a luxurious and sophisticated appearance.
Overall, the application of 500-word wood grain aluminum profiles is diverse and can be seen in various industries, contributing to both functional and aesthetic aspects of different products and structures.
Defects and Solutions of Powder Coating on Aluminum Profile
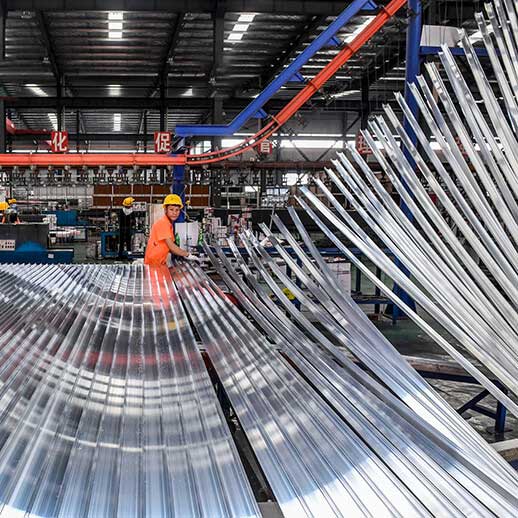
Firstly: Color Difference
Causes of defects:
1. Uneven coating thickness of aluminum profiles;
2. Not uniform temperature distribution of the aging oven;
3. Simultaneous production of goods with different materials, thicknesses, shapes and sizes;
4. Before changing the powder paint, the powder feeding device, spray gun, spray room and powder recovery are not be cleaned;
5. Color difference caused by poor distribution of powder and paint.
Solutions:
1. Ensure that the thickness of the coating film on the aluminum profile is uniform;
2. The temperature distribution of the aging oven is uniform;
3. Classify the goods according to the material, thickness, shape and size;
4. Clean all materials and devices before changing the powder paint;
5. Improve the quality of the powder and ensure that the L, a, and b of the powder are not much different and their positive and negative are uniform.
The Future Trend of Green Environmental Protection by Replacing Wood with Aluminum —— All Aluminum Home Furnishings
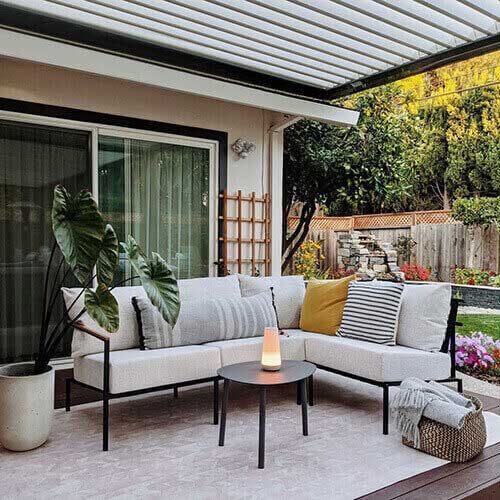
Nowadays, more and more people accept the green and environmentally friendly light steel houses. And more and more light steel villas have become the first choice for many people. Meanwhile, the green and environmentally friendly all-aluminum homes are also favored by residents. Afterwards the popularity of light steel villas, why all-aluminum homes are also popular?
Basic Knowledge of Aluminum Profiles
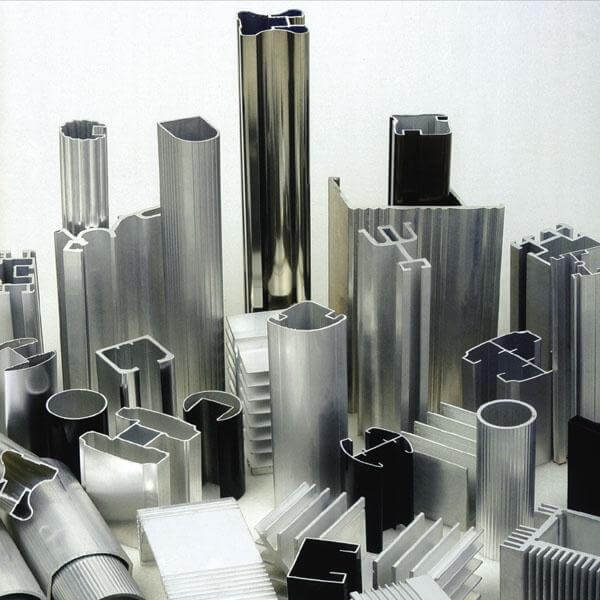
Aluminum profiles can be classified according to their applications:
1. Industrial aluminum profiles: mainly used in airplanes, trains, industrial heat sink, automobiles, electrical appliances, etc.
2. Aluminum alloy building profiles: mainly used for building doors and windows, curtain walls, indoor and outdoor decoration and aluminum profiles for building structures.
Aluminum profiles can be divided by different surface treatments:
1. Anodized aluminum profile: the profile surface is anodized, electrolytically colored or organically colored.
2. Electrophoretic painted aluminum profile: the surface of the profile is treated by anodized together with electrophoretic painting.
3. Powder coating aluminum profile: the surface of the profile is coated with thermosetting organic polymer powder.
4. Fluorocarbon spraying aluminum profile: the surface of the profile is coated with polyvinylidene fluoride paint. At present, the commonly used heat-insulating profile is an aluminum alloy profile that is threaded or poured.
INTOP ALUMIUM FACTORY
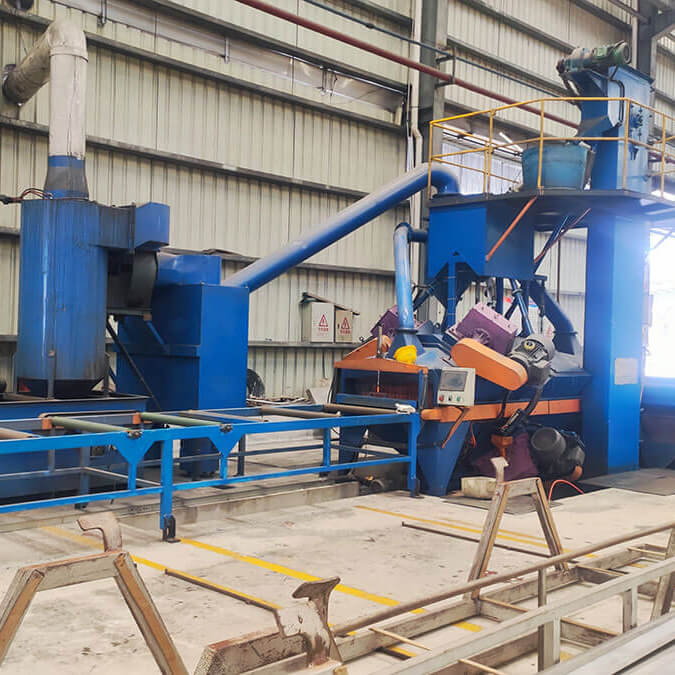
Now please allow me to make a brief introduction to our company and products.
We Intop Metal factory established in 2015, is located at Tian’an centre, Jihua Dong Road, Nanhai District, Foshan City, Guangdong Province, China, covering an area of 60,000 square meters, of which there are not less than 300 workers. Production equipment is the hard power for manufacturers. We have introduced lots of advanced production lines in our workshops, for example, 3 sets of casting ovens, 2 sets of aging ovens, 10 sets of extrusion lines, 1 set of horizontal anodizing line, 2 sets of powder coating line, one for vertical and the other for horizontal, and 2 sets of transfer wood grain lines.
Aluminum extruded profiles
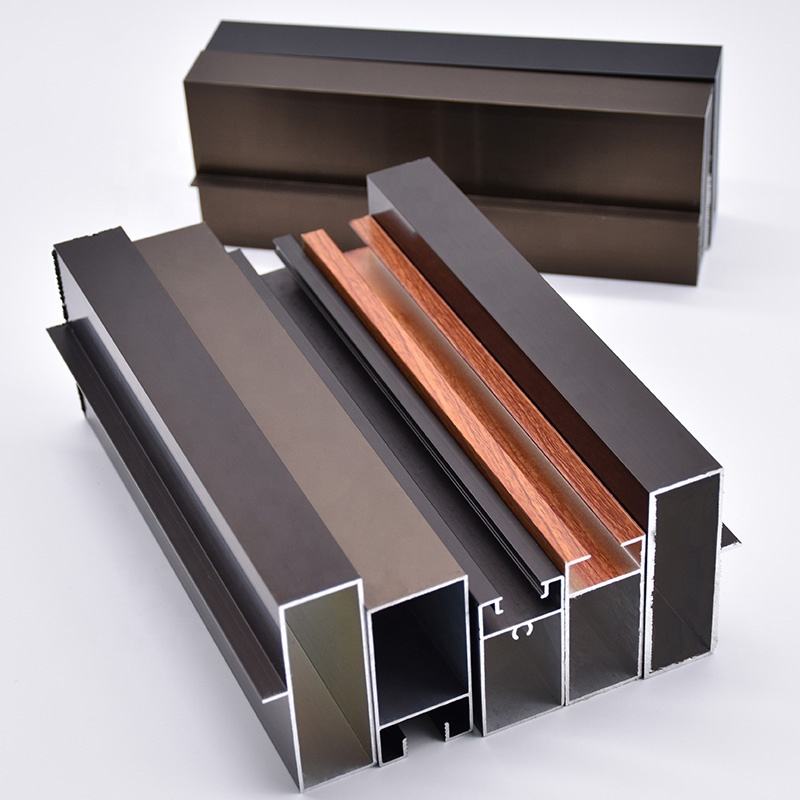
Aluminum profiles are extruded sections of aluminum that have a variety of cross sectional shapes. They are commonly used in construction, manufacturing, and engineering industries due to their lightweight, corrosion resistant, and high strength properties.
INTOP METAL ALUMINUM factory in FOSHAN GUANGDONG
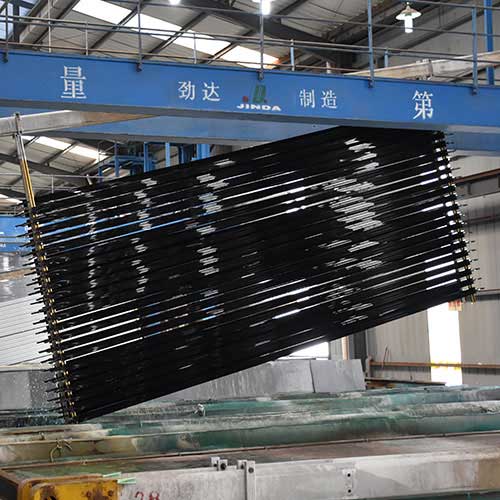
Our factory is located in Nanhai District Foshan City, which is one of the most professional gathering places for aluminum profiles in China. You can find many factories of aluminum profiles in Nanhai, but our factory is highly competitive in aluminum profiles in this industry. We have complete advanced production lines as below: 12 extrusion lines, 2 powder coating lines, 2 anodizing line, 2 transfer wood grain line, 1 mechanical polishing production line, 3 sandblasting production lines. We are a large-scale manufacturer of aluminum profiles for windows and doors and aluminum industrial profiles, covering 80,000 square meters, with annual output up to 38,000 tons.